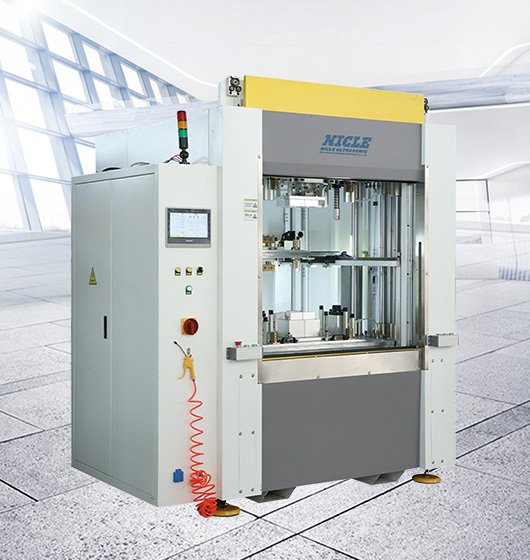
In the fast-evolving automotive industry, producing high-quality car lights—such as headlights, taillights, and fog lights—requires advanced welding technologies to ensure durability, precision, and efficiency. Among the top solutions, soldadoras de chapa caliente y máquinas de soldadura por ultrasonidos stand out for their ability to join thermoplastics like polycarbonate (PC) and polyamide (PA), commonly used in car light assemblies. This article explores how hot plate welding machines for car lights compare to máquinas de soldadura por ultrasonidos, their applications, and why they’re critical for automotive OEMs like Tata Motors, Yanfeng, and SAMIL in markets like India, China, and the U.S.
Hot Plate Welding Machines for Car Lights: How They Work
A soldadora de chapa caliente uses a heated plate to soften the surfaces of two plastic components, which are then pressed together to form a strong, hermetic seal. This method is ideal for larger, complex car light assemblies, such as polycarbonate headlight housings or taillight lenses, where precision and structural integrity are essential. Hot plate welding offers excellent bond strength and is suitable for parts requiring high-temperature resistance, making it a staple in automotive manufacturing. However, it can be slower and energy-intensive compared to other methods, with cycle times ranging from 10–60 seconds per joint.
Ultrasonic Welding Machines: A Faster, Eco-Friendly Alternative
In contrast, an máquina de soldadura por ultrasonidos leverages high-frequency vibrations (20–40 kHz) and pressure to instantaneously melt and bond thermoplastics, completing welds in just 0.1–1.0 seconds. This technology is perfect for smaller, intricate car light components, such as PC or ABS connectors and seals, offering 30% energy savings compared to traditional methods like hot plate welding. Our máquinas de soldadura por ultrasonidos eliminate adhesives, produce zero emissions, and meet stringent environmental standards like India’s FAME-II and China’s BS6, making them ideal for sustainable automotive production. For instance, Tata Motors and Yanfeng benefit from our precision bonding for EV headlights and taillights, reducing costs and enhancing efficiency.
Comparing Hot Plate and Ultrasonic Welding for Car Lights
Mientras que hot plate welding machines for car lights excel in creating robust seals for large, complex assemblies, they require more energy and time, potentially increasing production costs. Conversely, máquinas de soldadura por ultrasonidos offer speed, energy efficiency, and environmental benefits, making them a preferred choice for high-volume, eco-conscious manufacturers. For car lights, ultrasonic welding is particularly effective for thin, delicate PC and PA parts, while hot plate welding suits larger, structural components. Combining both technologies can optimize production lines, but ultrasonic welding’s 30% energy savings and no-adhesive design align better with modern automotive demands.
Applications in the Automotive Industry
Both technologies are critical for car light manufacturing. Hot plate welding ensures durability for headlight housings, while ultrasonic welding provides precision for smaller seals and connectors. In India, where two-wheelers and EVs are booming, our máquinas de soldadura por ultrasonidos support Tata Motors and SAMIL in producing lightweight, cost-effective car lights. In China, Yanfeng leverages our equipment for BS6-compliant EV components, reducing carbon footprints.
Why Choose Our Ultrasonic Welding Machines?
Our máquinas de soldadura por ultrasonidos save 30% energy, deliver precision for PP, ABS, and PC car lights, and meet global standards. Contact us at [Your Email] or [Your Phone Number] to explore how we can enhance your car light production with sustainable, efficient solutions.
#AutomotiveWelding #CarLights #HotPlateWeldingMachine #UltrasonicWeldingMachine #SustainableManufacturing